The use of the term “robot” was avoided in the early days of the invention of the robotic arm. It was simply because there was an unreal, almost movie-like connotation surrounding it. The inventors feared that such a connotation would hinder the adoption. However, as technology advanced and people were more accepting of automation, the use of the term “robot” eased its way into the industry.
In this blog post, we will discuss the history of robotic arms and dissect the different improvements made since their first appearance.
Early Modern Robots and Robotic Arms
The concept of robots, as we know it today, has evolved over time to describe machines that can mimic aspects of human intelligence and performance to complete tasks. It is difficult to choose a single point of invention that led to the development of modern robots.
However, here are some stages in history that marked important milestones in the conceptualization of the first robot:
The earliest conceptions of the robot can be traced back to Aristotle’s speculation in his book Politics(ca. 322 BC) that automata could lead to the abolition of slavery and promote human equality. One of the first verifiable versions of automation was found in the sketches of Leonardo da Vinci around 1495.
In the 18th century, a French toymaker named Jacques de Vaucanson built a mechanical duck that could imitate the movements of living beings. In the 19th century, a Japanese craftsman called Hisashige Tanake invented a range of complex mechanical toys, some of which could do simple automated actions.
The earliest industrial robots were produced around the 1930s in the United States where inventors began to experiment with manipulators that had their joints modeled on human shoulder-arm-wrist movements to replicate motions like pulling, pushing, pressing, and lifting. In 1938, Willard V. Pollard registered the first patent application for a mechanical arm which was termed the “Position Controlling Apparatus”.
In 1954, George Devol built the first digitally operated and programmable robot called the Unimate robot. This invention represented the foundation of the modern robotics industry, and Devol sold the first Unimate machine to General Motors in 1960.
When Was the First Robot Arm Built, and Why?
George Devol and Joseph Engleberger founded the world’s first robot company, Unimation, an abbreviation of “universal automation” in 1962. Unimate- which came to become the first commercially successful robotic arm was the initial industrial robot developed by this company. Unimation went on to build other robots which could assist the fast-growing automotive industry in welding and other applications.
The Unimate robotic arm played a crucial role in revolutionizing the manufacturing processes of the early 1960s by automating repetitive factory tasks. The automotive industry came to serve as a welcome market for robotic automation, where the newly developed Unimate first robot was used to simplify operations and reduce human effort. The robotic arm was also leveraged in other industries including electronics assembly, food and beverages, and metal manufacturing to improve the speed, precision, and consistency of production.
Characteristics of the First Robotic Arm
The Unimate robot was made up of a mechanical arm with several joints, and a gripper at the end. It could be programmed to perform functions like picking, moving, and assembling components. This revolutionary invention featured a 3-axis arm that could handle parts up to 226 kg. Equipped with hydraulic actuators, the Unimate could hold force constant due to the incompressibility of fluids (Inst Tools, 2019). The robot promised the ability to execute multiple tasks from material handling to welding. However, the invention proved to be a double-edged sword. While it alleviated the work hazards for humans, it created another problem of mass unemployment if adopted. Thus, companies hesitated to move forward with the technology.
Early Adoption of Robotic Arms: The Beginning of Industrial Robots
Let us go through the chronology of events- from the first robot arm to the widespread use of industrial robots as we know them today.
The Beginning
In 1961, Unimate introduced the very first industrial robotic arm. Joseph Engelberger and George Devol are to thank for this. Devol developed the patent that was granted in 1961. Engelberger functioned as the entrepreneurial half of the duo who founded Unimation. Thus, while Devol was the one who conceived the idea for the arm, Engelberger was thought to be the “father of the robot”.
Characteristics of the First Robotic Arm
This revolutionary invention featured a 3-axis arm that could handle parts up to 226 kg. Equipped with hydraulic actuators, the Unimate was able to hold force constant due to the incompressibility of fluids (Inst Tools, 2019). The robot promised the ability to execute multiple tasks from material handling to welding. However, the invention proved to be a double-edged sword. While it alleviated the work hazards for humans, it created another problem of mass unemployment if adopted. Thus, companies hesitated to move forward with the technology.
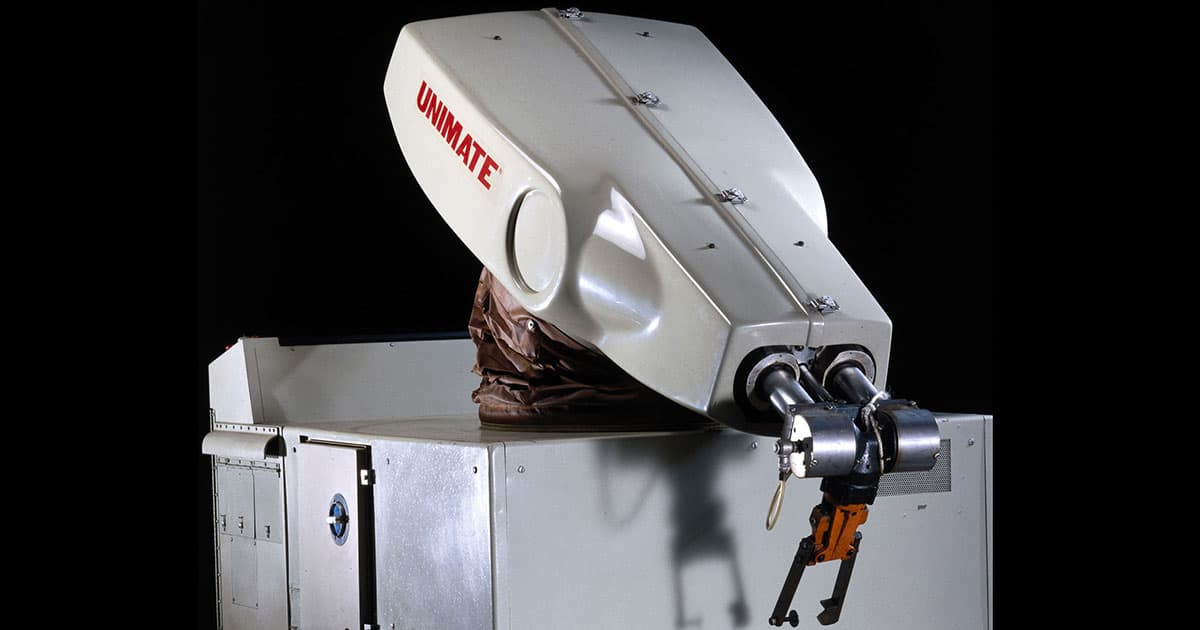
Figure 1: First Unimate Robotic Arm (1961) Image by IEEE
Early Adoption of Robotic Arms
Despite the fear of displacing workers, companies recognized the importance of keeping up to speed with automation. The industrial robotic arm became the perfect solution for companies in growing industries. Ultimately, companies are profit-driven and the fear of mass displacement waned over time. Many of the early adopters came from the West and Japan. The very first industrial robotic arm was installed in the General Motors factory in Trenton, USA. (Gasparetto et al., 2019). This arm weighed 4,000 points and cost General Motors $25,000- which was the first robotic arm price.
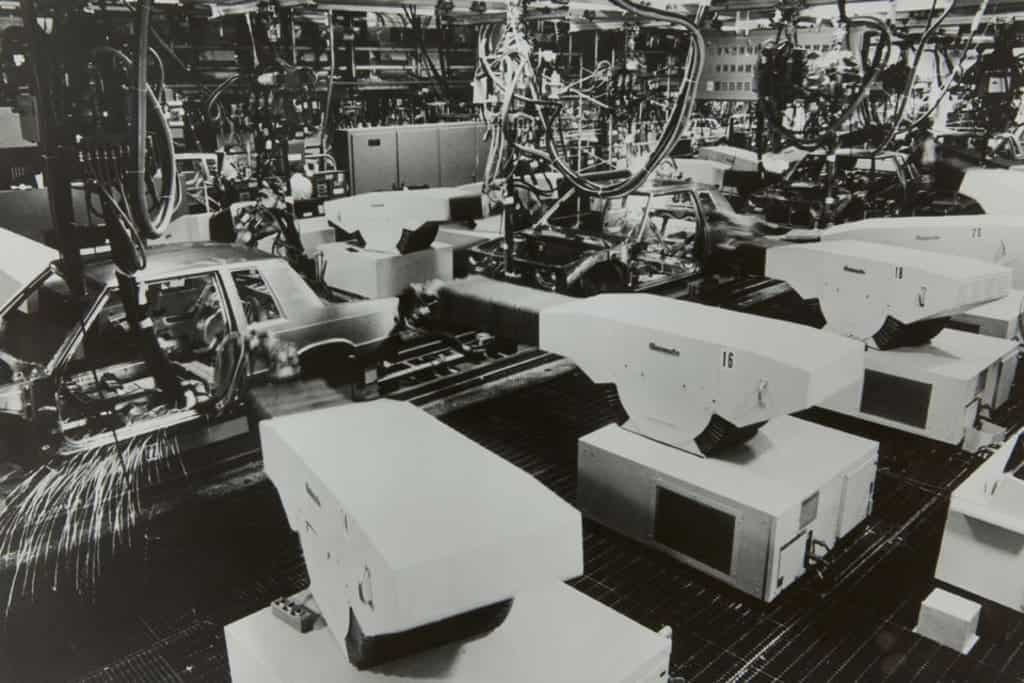
Figure 2: Unimate in General Motors Factory from Journal
Further Developments
However, robotics arms as we know it did not stop at just 3-axis. Robots underwent constant refinement and improvements to stay relevant.
The History of Robotic Arm Innovation: Wave 2
This wave lasted approximately 9 years from 1968 to 1977. It was characterized by having servo-controllers enabling point-to-point motion. The robot was also programmable with a teach box. However, each robot had a specific software and could only perform a specific task. Therefore, reducing the versatility of these robots.
A prominent alteration was the change from hydraulic to electronic actuators. Electronic actuators allow greater control over position and velocity. Additionally, simultaneous adjustments can be made with accuracy and repeatability exceeding that of hydraulic actuators (Tolomatic, 2017). Scheinman pioneered the electronically powered robotic arm. He was a mechanical engineer at Stanford who built the Stanford arm. The arm boasted 6-axes and sensors to ascertain the position and velocity of the joints. Furthermore, what was groundbreaking was the fact that the arm was easy to control and compatible with computer systems in that era (InfoLab Stanford, n.d.)
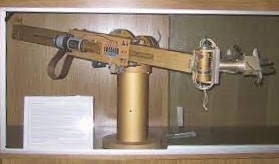
Figure 3: Stanford Arm Image by Stanford InfoLab
The History of Robotic Arm Innovation: Wave 3
From 1978 to 1999, the “third-generation” industrial robots were commonly classified by their ability to perform complex tasks. Many additional features were included to enhance the overall functionality of the robot.
Firstly, robot movements could account for environmental changes. This was especially crucial in a factory setting where the arms might require relocation. Secondly, robot arms were now able to run diagnostics and provide indications of where and what type of failure had occurred. The ability to run diagnostics significantly reduces the time needed to locate errors. Lastly, robot arms were now able to perform complex tasks. For instance, data used from vision or perception systems (from the sensors or cameras) allowed the robot to perform tactile inspection and assembly operations.
Types of Robots Today
Robotics arms as we know it did not stop at just the 3-axis. Robots underwent constant refinement and improvements to stay relevant. Here are some popular types of robots being used these days:
Humanoid Robots
Humanoid robots are automated machines built to resemble humans in form and function. They typically have parts that resemble human features such as heads, torsos, arms, and legs. They incorporate actuators to replicate muscle-joint movements and other sensors which allow them to perceive and interact with their surroundings autonomously. Their algorithms are based on a convergence of engineering and cognitive science to help them mimic human capabilities. Humanoid robots are designed for application in research, healthcare, customer service, entertainment, and other domains that require human-like interactions.
Industrial Robots
Industrial robots are heavy-duty machines designed to automate large-scale manufacturing operations. They are usually fixed in factories and utilized to perform repetitive tasks with speed and accuracy. Their sizable apparatuses usually consist of at least one arm-like manipulator that is capable of movement on three or more axes. They are programmed to perform industrial functions such as welding, painting, assembly, packaging, and material handling. Industrial robots increase the productivity of manufacturing processes and improve workplace safety by managing tasks that are hazardous and labor-intensive.
Cobots
Cobots or collaborative robots are designed to work alongside human beings in shared workspaces. Unlike conventional machines, cobots are fitted with advanced sensors and safety features that allow them to perform tasks within close proximity to humans. They can contribute to tasks such as assembly, pick-and-place, quality monitoring, and testing. Cobots can be programmed to support agile manufacturing environments by automating menial, repetitive, or physically intense activities. Their flexibility and seamless integration with pre-existing processes make them suitable for small-batch production and dynamic industrial settings.
Agricultural Robots
Agri-bots or agricultural robots are automated machines built to assist in various agriculture and farming tasks. They are usually employed in fields to automate repetitive, labor-intensive agricultural activities. These robots function as high-tech farming machines that could be involved in harvesting, irrigation, seeding, weeding, spraying fertilizers, and crop monitoring. They use advanced technologies such as sensors, GPS, and AI to support modern-day precision agriculture and data-driven farm management practices. Agribots can increase the efficiency and productivity of agriculture while reducing labor costs, and optimizing resource usage.
Military Robots
Military robots are unmanned ground vehicles (UGVs) or unmanned aerial vehicles (UAVs) deployed for military applications. These robots are equipped with sensors, weapons, and communication systems that aid in performing tasks like intelligence gathering, navigation, data transmission, and surveillance. Military robots are programmed to function as autonomous or remote-controlled machines which play a crucial role in modern warfare. They can take over challenging military activities such as delivering targeted attacks, bomb disposal, and offering logistical support in risky military posts.
Nanorobots
Nanorobots are tiny machines created to complete specific tasks at the nanoscale. These microscopic robots are built by assembling one individual atom at a time and can range from 50 to 100 nanometers in size. They can be built from organic or artificial materials, such as DNA molecules, peptides, silicone, or graphene. Nonorobots are fitted with nanoscale parts that help in their propulsion, sensing, and movement to fulfill targeted tasks. They can perform a wide variety of applications such as targeted drug delivery, cancer treatment, environmental cleanups, and molecular-level manufacturing.
Integration of AI in Robotic Arms
According to CNBC, we are currently in the golden era of robotics adoption (Gurdus et al., 2019). Rising labor costs coupled with the need to meet rising demands have propelled the adoption of robotic arms.
Presently, robotic arms can have up to 7-axis and companies are spearheading change through the simplifying of programming processes. Such innovations address the pain points of many manufacturing companies and carve a way for people with no programming background to adopt such technology. Additionally, the mistakes in the work cell can be predicted beforehand and avoided with the introduction of offline programming.
The adoption of AI and machine learning algorithms can automate the functions of robotic arms with better precision and consistency. Accordingly, the reduction in programming downtime increases the overall efficiency of companies. Platforms like Augmentus are pioneering robotic technologies that enable easy and rapid robotic automation. Their incorporated algorithms allow even those with no programming experience to build dynamic industrial robots within minutes.
Conclusion
Innovators are dedicated to developing robots with varying features, and capabilities. Robots are expected to provide improved performance over time by integrating AI and machine learning tools. Cobots have become increasingly popular as they can be used alongside human workers without the need for caging or safety equipment. Companies pioneering the production of cobots include Universal Robots and Rethink Robotics.
With the demand for cobots expanding, manufacturers can reap economies of scale and lower the costs of accessing such cobots. Therefore, the barrier to entry for using robotic arms or cobots in manufacturing processes is the ease of use rather than cost. Augmentus solves this problem with algorithms that enable fully automated path generation and an intuitive graphical interface that eliminates the need for coding in robot teaching.
Companies using Augmentus have experienced up to 70% cost reduction and 17 times faster deployments across a wide variety of applications, such as spraying, palletizing, welding, and inspections. Augmentus ushers in a new era of human-machine interface, democratizing robotic automation.
Discover how Augmentus is advancing robotic programming with intuitive, no-code solutions.
FAQ
What are the primary functions of robotic arms in the industry today?
Robotic arms in today's industry primarily automate tasks like welding, painting, assembly, and material handling. They enhance productivity, improve precision, and ensure workplace safety by managing hazardous tasks. With their flexibility, they support efficient manufacturing and contribute to cost reduction by optimizing resources and reducing the need for labor.
How has AI influenced the design and functionality of modern robotic arms?
AI has significantly influenced modern robotic arm design and functionality. It enables automation with precision and adaptability to changing environments. AI-driven predictive maintenance reduces downtime, and simplified programming processes make deployment accessible to individuals without programming backgrounds. AI also facilitates collaborative work between robotic arms and human workers, giving rise to collaborative robots (cobots).
What makes Augmentus’ robotic programming software stand out in today’s market?
Augmentus' robotic programming software stands out with its fully automated path generation, eliminating manual coding. Its intuitive graphical interface simplifies programming for users. Predictive capabilities prevent errors, and rapid deployment reduces setup times. It also significantly reduces costs, making robotic automation more accessible to manufacturers by lowering entry barriers.
About Augmentus
Augmentus pioneers industry-leading robotic technologies that enable easy and rapid robotic automation, enabling anyone, even those with no robotic experience, to program dynamic industrial robots in minutes. Our proprietary technology incorporates algorithms to enable fully automated robot path generation and an intuitive graphical interface that eliminates the need for coding and CAD files in robot teaching. Companies using Augmentus have experienced up to 70% cost reduction and 17 times faster deployments across a wide variety of applications, such as spraying, palletizing, welding, and inspections. Augmentus ushers in a new era of human-machine interface, democratizing robotic automation.
References
Gasparetto, A., & Scalera, L. (2019). A Brief History of Industrial Robotics in the 20th Century. Advances in Historical Studies, 08(01), 24–35. https://doi.org/10.4236/ahs.2019.81002
Gurdus, L. (2021, December 14). “Golden era of robotics adoption” kicks off in 2022, strategist says. CNBC. https://www.cnbc.com/2021/12/14/golden-era-of-robotics-adoption-kicks-off-in-2022-strategist-says.html
InfoLab Stanford. (n.d.). Robot. http://infolab.stanford.edu/pub/voy/museum/pictures/display/1-Robot.htm
Inst Tools. (2019, March 21). What is a Hydraulic Actuator? https://instrumentationtools.com/what-is-a-hydraulic-actuator/
Tolomatic. (2017, June 20). High force linear actuators – hydraulic vs electric [WEBINAR]. https://www.tolomatic.com/de-de/blog/artmid/843/articleid/337/high-force-linear-actuators-%E2%80%93-hydraulic-vs-electric-webinar#:%7E:text=An%20electric%20linear%20actuator%20with,those%20of%20a%20hydraulic%20system.